Tantalum is a metal element with the element symbol of Ta, an atomic number of 73, a density of 16.68g/cm, and a melting point of 2980 DEG C. Pure tantalum with blue color and excellent ductility can be rolled into a very thin plate in the cold state without intermediate annealing.
Tantalum has a series of excellent properties such as high melting point, low vapor pressure, and cold processing performance, high chemical stability, anti-corrosion ability, constant liquid metal oxide film, which has important applications in electronics, metallurgy, chemical industry, aerospace, medical health, and scientific research and other high-tech fields.
Discovery history
In the middle of the Seventeenth Century, a heavy black mineral was found in North America and was sent to the British Museum. After about 150 years, until 1801, the British chemist C.Hatchett accepted the analysis task of the ore in the British Museum, discovered a new element, and named it columbium, which is to commemorate the earliest discovered mineral areas — Columbia.
In 1802, when the Swedish chemist A.G.Ekaberg analyzed a mineral in Scandinavia, making their acid fluoride salt after recrystallization, leading to the discovery of the new element, he named the element tantalum referred to in Greek mythology, Jose Tantalus, the son of God’s name.
Due to the nature of columbium and tantalum being very similar, people once thought that they are the same kind of elements. In 1809, the British chemist William Hyde Wollaston compared tantalum and Columbium oxide, although different density value, he believes that the two are identical materials.
In 1844, the German chemist Heinrich Rose dismissed the conclusion that tantalum and Columbium are the same element, and identified that they are two different elements by chemical methods. He named them “Niobium” and “Pelopium”.
In 1864, Christian Wilhelm Blomstrand, and Louis Joseph Troost clearly demonstrated that tantalum and niobium are two different chemical elements, and determine the chemical formula of some related compounds. The early tantalum metal has more impurities. Werner von Bolton was first made pure tantalum metal in 1903.
Scientists first extract tantalum from niobium with the method of hierarchical crystallization, which is found by de Marinilla in 1866. Today, scientists are using a solvent extraction method for the solution containing fluoride.
Preparation technology
The preparation of tantalum is the process of reducing pure tantalum compounds to metal tantalum. The raw materials are five tantalum oxide, tantalum chloride, five tantalum fluoride, and fluoride (such as K2TaF7,). The reducing agent is sodium, magnesium, other active metals, and carbon and hydrogen. The melting point of tantalum is as high as 3669K, so it is powder or spongy metal after reduction. It is necessary to further smelting or refining, in order to get dense metal.
The tantalum preparation methods are sodium thermal reduction, carbon thermal reduction, and molten salt electrolysis. Sodium thermal reduction of potassium tantalate is the most widely used method of tantalum production in the world.
The tantalum powder has a complex shape and a large specific surface area. Carbon thermal reduction of five oxidation of tantalum has been an industrial method for the production of tantalum, but because the purity of the product is not high enough, is not as widely used as the sodium reduction method. The molten salt electrolysis method is divided into two ways: electrolyte electrolysis and oxygen-free electrolyte electrolysis. Molten salt electrolysis can only produce metallurgical grade tantalum powder. Five hydrogen fluoride reduction is considered to be one of the most promising methods for tantalum production, but it has not been used in industrial production because of the high requirements of equipment material and environmental protection.
The majority of tantalum powder is directly used for tantalum capacitors in the electronic manufacturing industry, so the tantalum milling process, such as the preparation of tantalum metal is also from tantalum and tantalum powder by vacuum heat treatment, capacitor grade tantalum powder hydrogenation method category.
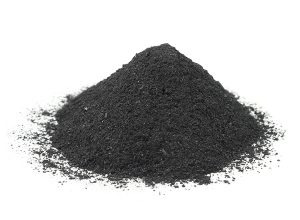
Production of tantalum powder
Sodium metal thermal reduction method is an important method for the production of tantalum powder, which is the main method of industrial production of tantalum powder (including metallurgical Ta powder). The particle shape of metal tantalum powder with the large surface area is complex, which is suitable for anode material for tantalum electrolytic capacitors by electron beam melting and vacuum arc melting of tantalum or tantalum sintered in vacuum refining, then the high purity tantalum rod made and then processed into a variety of tantalum.
Since the 1970s, it has been widely used to increase the specific capacitance of tantalum powder. The commonly used doping agent is phosphate, which can be mixed before or after the crystallization of potassium fluoride and can be added before the vacuum heat treatment of tantalum powder. The doping can prevent the sintering of tantalum powder during the sintering of the tantalum anode block, thus avoiding the reduction of the specific surface area of the tantalum anode block. We can remove oxides from metal sodium with the metal-ceramic filter or cold trap method.
The process of reduction of potassium and sodium fluoride in an inert atmosphere at 1153 ~ 1173K temperature and the reduction products are metal tantalum powder, potassium fluoride, sodium fluoride, and diluent which are not involved in the reaction.
Before the 1950s, the solid metal sodium and potassium fluorotantalate layer was placed in the reactor of bomb explosion reduction reaction, although the product of tantalum powder is fine particle size, large surface area, oxygen, and carbon content is high, no practical value.
With tantalum capacitors being small and micro, the corresponding need to adopt more surface area tantalum powder, mainly used in the liquid reduction, mainly supplemented by mixing sodium, doping technology, the volume rate of tantalum powder increased to 1000uF – V yield every year.
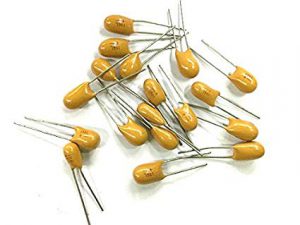
The fluoride was removed by dipping, and then washed with HCl18% and HF1% solution at 1 2H for 363K, then washed with pure water and dried at 353K temperature. For the preparation of capacitor grade tantalum powder, tantalum powder should be the original size distribution, vacuum heat treatment (see tantalum powder vacuum heat treatment), crushing and screening and modulation post-processing, if necessary, will also increase the magnesium reduction deoxygenation, pickling, washing and plastic processing, in order to obtain high quality and low and high specific capacitance of capacitor grade tantalum powder.
It is expected that the continuous improvement and development of tantalum powder produced by sodium reduction is the result of the miniaturization, miniaturization, and cost reduction of electronic products. Since the 1960s, the specific capacitance of tantalum powder has been increasing, and the capacitance ratio of tantalum powder has reached 22000~26000uF•V/g in the United States, Japan, Germany, and other countries.
Stanford Advanced Materials supplies high-quality tantalum products to meet our customers’ R&D and production needs. Please visit http://www.samaterials.com for more information.
Recent Comments