Introduction
Tantalum crucibles are revered for their exceptional properties in high-temperature applications. Yet, they undergo a meticulous manufacturing journey to ensure precision and adherence to stringent quality standards. The production of these crucibles involves a series of advanced processes. These products marry the unique characteristics of tantalum with the exacting requirements of diverse industries. Let’s learn about these complex manufacturing processes step by step.
1. Raw Material Selection:
The journey begins with the careful selection of tantalum raw materials. High-purity tantalum powder is often used, so the crucibles can maintain their integrity and resist contamination in demanding environments.
2. Powder Metallurgy:
Next, powder metallurgy takes center stage. Tantalum powder undergoes compaction and sintering at this stage. This process forms the crucible’s initial shape and leverages tantalum’s exceptional ductility and high melting point.
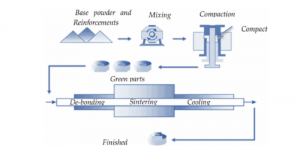
3. Cold and Hot Working:
Third, cold and hot working techniques are employed to refine the crucible’s shape further. Cold working involves processes like rolling and forging. Hot working is often conducted at elevated temperatures and imparts the desired final geometry.
4. Machining and Precision Cutting:
Precision machining techniques also come into play to achieve the specific dimensions required for various applications. With Computer Numerical Control (CNC) machining, accuracy is achieved and advanced cutting tools shape the tantalum crucibles with meticulous detail.
5. Heat Treatment:
Heat treatment is a critical step. It optimizes the mechanical properties of the tantalum crucible. Controlled heating and cooling processes enhance the crucible’s strength, durability, and resistance to deformation.
6. Surface Finish and Coating:
Surface finishing techniques, such as polishing or coating, are applied to meet the desired surface characteristics. This not only enhances the crucible’s aesthetic appeal but also improves its resistance to corrosion and chemical interactions.
7. Quality Control Measures:
Throughout each stage, rigorous quality control measures are implemented. Non-destructive testing methods ensure that the tantalum crucibles meet the highest standards for integrity and performance. They include ultrasonic and radiographic examinations.
8. Welding and Joining Techniques:
Welding and joining processes with tantalum welding material are employed to create seamless connections in complex crucible designs. This ensures structural integrity and minimizes the risk of contamination in applications where purity is paramount.
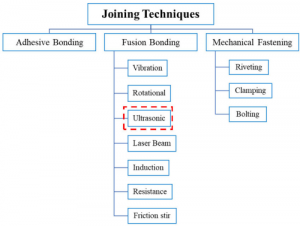
9. Final Inspection:
Last, each tantalum crucible undergoes a comprehensive final inspection. Dimensional accuracy, surface quality, and overall performance are scrutinized, so that the crucibles meet or exceed industry specifications.
10. Traceability and Documentation:
Traceability and documentation are integral components of the manufacturing process. Each tantalum crucible is meticulously tracked. Comprehensive documentation ensures transparency in the supply chain and facilitates compliance with industry standards.
Conclusion
In a word, the manufacturing of tantalum crucibles represents a fusion of advanced metallurgical techniques, precision engineering, and stringent quality control. The product obtained not only harnesses the exceptional properties of tantalum. It also meets the diverse and demanding needs of industries where high-performance crucibles are indispensable. For more information, please check our homepage.
Reference:
[1] HG, Prashantha & Xavior, Anthony. (2018). Processing of Graphene/CNT-Metal Powder. 10.5772/intechopen.76897.
[2] Bhudolia, Somen & Gohel, Goram & Leong, Kah Fai & Islam, A.. (2020). Advances in Ultrasonic Welding of Thermoplastic Composites: A Review. Materials. 13. 10.3390/ma13061284