Introduction
In the realm of riveting applications, the bucking bar is an often-overlooked but critical component. This component is crafted from different materials, and these advanced materials can significantly impact its effectiveness, including absorbing vibrations and facilitating a secure, seamless riveting process.
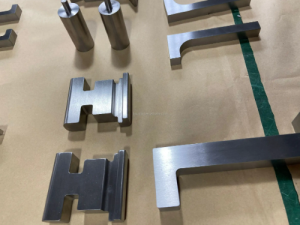
This guide explores the importance of bucking bar material selection. Hope that you can learn about key considerations for optimal performance in riveting applications.
Understanding the Role of Bucking Bars:
Bucking bars are also known as rivet sets. They serve as the counterforce in riveting operations. While the rivet gun drives the fastener into place, it ensures that the force is distributed evenly.
These devices prevent distortion of the workpiece and facilitate a strong, reliable joint. The bucking bar material directly influences its ability to absorb energy, resist wear, and deliver precision in rivet forming.
Common Bucking Bar Materials:
They come in a variety of materials. Each comes with its unique properties and advantages:
- Steel: Traditional steel bucking bars stand out for their durability and relatively low cost. They come in various shapes and sizes to accommodate different rivet types. However, they can be heavy and may transmit vibrations more than some alternative materials.
- Tungsten Alloy: Tungsten alloy bucking bars strike a balance between weight and durability. Their high-density composition allows for more compact designs without sacrificing effectiveness. They are particularly useful in applications where access space is limited.
- Copper: Copper ones are favored for their softer nature, so they are suitable for preventing surface marring on delicate materials. While they may wear more quickly than steel or tungsten, their use is essential in situations where protecting the workpiece is paramount.
- Lead: Lead components provide a non-marring option, especially in aerospace applications where surface damage is unacceptable. They are soft and deformable. They can ensure minimal impact on the workpiece while still effectively absorbing energy.
1. Weight Considerations:
The weight of the bucking bar is a crucial factor in material selection as well:
- Heavy-Duty Applications: In heavy-duty applications, such as construction or shipbuilding, maximum force is often required. Under these conditions, steel or tungsten alloy bucking bars are preferred due to their weight and durability.
- Precision Work: For applications that demand precision and accessibility, tungsten or copper components offer a more manageable and wieldy option since they are lighter than steel.
2. Vibrational Damping Properties:
Additionally, the ability of a bucking bar to absorb and dampen vibrations is vital for user comfort and safety:
- Tungsten Alloy: W alloy is notable for its excellent vibrational damping properties. This alloy reduces the impact on the operator and leads to a more comfortable and controlled riveting experience.
- Steel: While steel is durable and effective, it may transmit more vibrations compared to materials with better damping properties. It potentially leads to operator fatigue during prolonged use.
3. Application-Specific Considerations:
Tailoring bucking bar material to the unique demands of the application is key:
- Aerospace: Aerospace applications often require non-marring materials like copper or lead to prevent surface damage on sensitive materials, coupled with tungsten for its weight-to-size ratio.
- Automotive: Steel or tungsten alloy bucking bars are commonly used in automotive assembly. They offer a balance between weight, durability, and cost-effectiveness.
4. Maintenance and Wear Resistance:
Considering the wear characteristics of the material ensures longevity and reduces replacement frequency:
- Steel: Steel comes with durability. Such bucking bars are resistant to wear and deformation. They have become suitable for high-volume production environments.
- Copper and Lead: These softer materials are more prone to wear but excel in applications where preventing surface damage is crucial.
Conclusion:
In the world of riveting, the choice of bucking bar material is quite diverse. Impacting factors include weight, vibrational damping, wear resistance, and application-specific requirements. The optimal one strikes a balance between these factors, forging success in riveting applications by enhancing precision, durability, and user comfort.
As industries continue to evolve, the careful selection of bucking bar materials remains a critical element in achieving efficient and reliable riveting processes.
Advanced Refractory Metals (ARM) specializes in the manufacturing and distribution of top-notch tungsten bucking bars in diverse shapes and dimensions. ARM comes with over 20 years of experience and top-quality products. Send us an inquiry if you are interested.