Since the 1950s, TZM alloy (Mo-0.5 Ti-0.1 Zr-0.02 C) has been developed to meet the needs of the nuclear power system, aviation, and aerospace industry. It is the most widely used molybdenum alloy in the industry and the earliest refractory alloy used as a high-temperature structural material. However, the low-temperature brittleness of molybdenum alloy greatly limits its application.
Tantalum metal has a lower plastic brittle transition temperature (196 ℃) and has better performance on the workability, weldability, ductility, and oxidation resistance at room temperature than that of molybdenum and tungsten in refractory metals. In addition, tantalum and its alloys with high melting point (2996 ℃), corrosion resistance, excellent high-temperature strength, and free of radioactive, etc, are widely used in the electronics industry, chemical industry, aerospace, weapon system, and the medical field, etc.
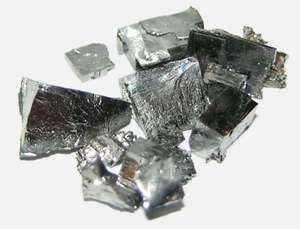
The applications of tantalum materials in the electronics industry mainly include tantalum capacitors, integrated circuits, electron tubes, memory devices, and passive devices.
Tantalum capacitor
Tantalum has the metal property of a valve, and the compact oxide film formed on its surface has unidirectional conductivity, which is suitable for making capacitors. Tantalum capacitors have a large capacity and small volume, and their capacitance is three times that of aluminum capacitors, but their volume is much smaller than that of aluminum capacitors. The working temperature of the tantalum capacitor ranges from -80 to 200 ℃, which can meet the demand of different temperatures. Besides, tantalum capacitors have strong stability and heat resistance performance and become a kind of material with high reliability in the electronics industry, which is widely used in military and high-tech fields that need to ensure high reliability.
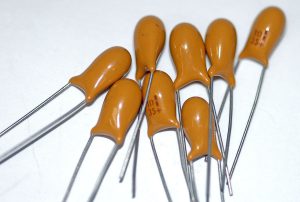
Integrated circuit
Tantalum material is introduced into the semiconductor industry as a barrier layer thin-film material used to prevent the diffusion of copper atoms to silicon wafers. There are no compounds are formed between copper and tantalum, and copper and nitride, so tantalum and tantalum base membranes are used as barrier layers to prevent copper diffusion, and the typical thickness of the barrier layer is 0.005 ~ 0.01μm. In order to prevent the diffusion of copper atoms into the silicon matrix, tantalum nitride, tantalum silicide, tantalum carbide, and silicon nitride are used as barrier layers.
Memory device
Tantalum oxide matrix resistive memory (RRAM) has the advantages of simple structure, fast read and write speed, strong instability, and compatibility with the CMOS process. The permittivity of tantalum oxide material is very high, which is about 25. Moreover, there are only two stable phases between ta-O, Ta2O5 and TaO2, which have high oxygen capacity ratio under the high temperature of 1000 ℃.
Passive device
When tantalum nitride film is exposed to air, the surface will naturally form a layer of the oxide layer to protect the film from erosion in the presence of water vapor and voltage. The chip resistance of tantalum nitride will not cause catastrophic failure of the device due to the poor integrity of the package or protective coating.
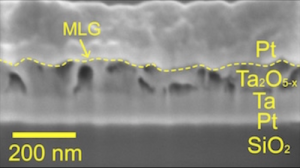
When researchers discovered tantalum’s high-temperature resistance, good ductility, and corrosion resistance, the research on tantalum metal began. At present, the application field of capacitor grade tantalum wire is further expanded with the rapid development of the electronic market. However, the development of tantalum capacitors is greatly restricted due to various reasons, such as the increase in production cost, the further consumption of resources, and the intensification of the competition between ceramic and other capacitors.
In recent years, the market consumption of capacitor tantalum wire has been maintained at about 160 tons per year. With the development and use of military capacitors and the miniaturization and chip type of capacitors, the capacitor-grade tantalum wire gradually develops toward the thick and thin poles.
Please visit http://www.samaterials.com for more information.